Since the physical and chemical properties of ceramics are quite different, the life calculation formula for steel bearings cannot be applied to ceramic bearings directly. Tests show that the actual endurance life of ceramic bearings and steel bearings under various working conditions are quite discrepant.
The following article presents the life comparison between steel bearing and various kinds of ceramic bearings under different working conditions, and the factors that affect the life of bearings.
I. Load - Life chart.
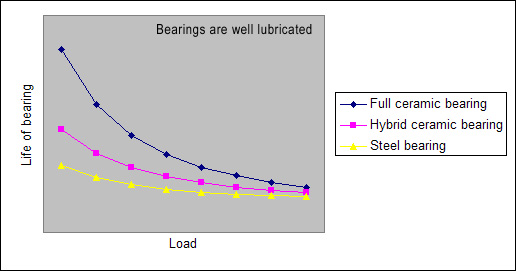
The full ceramic and hybrid ceramic bearings have significant longer life than steel bearings since the normal wear of ceramic on ceramic or ceramic on steel is much less than that of steel on steel. But due to the much higher rigidity of ceramics, the balls or races are not deformed under load. It generates much higher stress at the contact point between the balls and raceways, compared to steel bearing. With the increasing of load, the higher increasing of contact stress would pit/destroy the surface of steel races (for hybrid) or ceramic balls and ceramic races (for full ceramic) and cause premature failure. Therefore, under heavy load or even some impact load, the endurance life of a ceramic bearing could equal or even shorter than a steel bearing.
II. Endurance life of bearings in water.
Tests show that full ceramic bearings possess from 15 to 70 times longer endurance life than stainless steel AISI440C bearings. Full Si3N4 and ZrO2 ceramic bearings possess from 3.5 to 5 times longer life than hybrid bearings. Rolling life of all SiC ceramic bearings is approximately the same as hybrid bearings. Rolling life of ceramic bearings in water is mainly due to propagation of cracks, pitting and flaking.
The high chrome carbon steel bearings cannot be used in water.
III. Endurance ife of full ceramic bearings in corrosive environments.
It is important to choose the correct material of bearings for corrosive environments. The endurance life of a full ceramic bearing working in corrosive environments is shorten than in normal working conditions.
IV. Factors affected endurance life of bearings
1) Lubricating grease life
Lubrication is very important to rolling bearings. Insufficient lubrication would significantly shorten the rolling life of bearings. In environments that place high demands on the bearing
lubricant, bearings experience surface wear because of insufficient lubricant film. Bearings can fail if
the initial grease charge is not replenished within an
acceptable period of time. Ceramic bearings run cooler
and can operate with thinner lubricant films (ceramics are ceramic self-lubricated and with lower friction coefficient then steel on steel), so there is
less aging of the grease and the required relubrication
interval will be longer. The result is increased endurance life
compared to steel bearings in the same operating
conditions.
2)
Electrical arcing
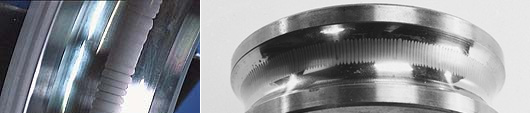
Static electricity emanating from charged belts or from manufacturing processes can pass through a machine's shaft and through a bearing to the ground. When this current bridges the lubrication film between steel balls and steel raceways, microscopic arcing occurs. This produces localized and extreme temperatures that melt the crossover point. Gradually a washboard
or fluting pattern appears on the rolling surface. And the bearing becomes unsmooth and generates excessive noise during running. Besides the surface damage, premature
aging of the lubricant also occurs. The natural
insulating properties of ceramic material avoids this
type of damage.
3) Vibration wear
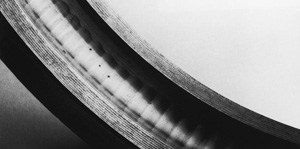
Bearings do not have to be rotating to be damaged in an application. When vital equipment has a standby back-up unit, damage can be experienced from transient vibrations caused by running machinery. Depending on the proximity of the idle unit to the unit in operation, vibrations generated from the running equipment can cause the rolling elements in the bearing of the static machine to vibrate. These create the condition of false brinelling, or a wearing away of the raceway surface in an oblong or circular shape. When the standby equipment is placed into service, the bearings usually will be noisy and require replacement.
For ceramic bearings, because
of the lighter weight ceramic balls and dissimilar materials,
the risk of false brinelling damage is much less (but cannot totally avoid).
4) Operating temperatures
The heat generated in bearings is attributable to viscous
friction from lubrication and load dependent friction
between the balls and raceways. The source of the loading
is external as well as internal. There is little that can
be done to reduce the external loads. However, since
ceramic balls have only 40% of the density of steel balls,
the centrifugal load generated by the balls is less and the
internal friction is lower. This provides cooler running for
the same operating conditions or, if applicable, a higher
rotational speed while maintaining the same temperature.
5) Wear from contamination
In contaminated environments, solid particles create
dents in the rolling surfaces and raised edges around
those dents. This condition causes noise and premature
wear as the steel balls roll over those surfaces. The much harder
ceramic ball material smooths the surface roughness
with no material removal. Also, there is little evidence of
adhesive wear as seen in steel bearings. This reduces the
noise and wear, which extends the bearing service life.
In conclusion, ceramic bearings have longer life duration in man when compared to steel bearings. But premature failures could happen in many cases. To analyse the causes of failure and eliminate the causes would extend the service life of ceramic bearings.
|